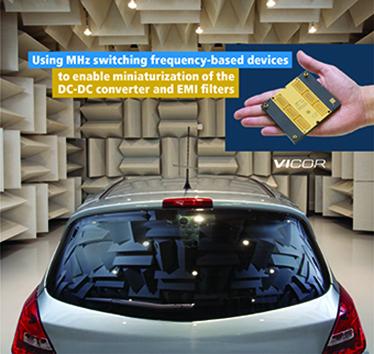
MHz switching frequency-based devices enable miniaturization of the DC-DC converter and EMI filters
Achieving EMI conducted emission compliance for automobiles with a single stage filter. By Nicola Rosano, Sr. Strategic FA/System Engineer at Vicor
More details...
A full brick package developed by TDK-Lambda, the PF1500B-360, is for high voltage distributed power architectures
More details...
.jpg)
The three-phase BLDC motor drive inverter uses the EPC2065 eGaN FET. It operates from an input supply voltage between 14 and 60V (nominal 48V) and is available in two configurations – a standard unit and a high current version.
The EPC9167 standard model is a three-phase BLDC motor drive inverter board featuring the EPC2065 eGaN FET rated at 3.6mΩ maximum RDS(on), 80V maximum. It uses single FETs for each switch position and can deliver up to 20A RMS maximum output.
The high current configuration (EPC9167HC) uses two paralleled FETs per switch position and can deliver up to 42A peak (30A RMS) maximum output.
Both versions contain all the necessary critical function circuits to support a complete motor drive inverter including gate drivers, regulated auxiliary power rails for housekeeping supplies, voltage, and temperature sense, accurate current sense and protection functions. They also include ST Microelectronics’ STDRIVEG600, smart motor drive GaN half-bridge driver.
The EPC9167 boards measure 130 x 100mm (including connector). They can be configured for multi-phase DC/DC conversion and support both phase and leg shunt current sensing. The reference boards demonstrate the benefits of a GaN-based motor drives, such as lower distortion for lower acoustic noise, lower current ripple for reduced magnetic loss, lower torque ripple for improved precision and lower filtering for lower cost, says the company. The boards’ weight and size enable them the drive to be incorporated into the motor housing; while supporting low inductance, higher power density motors.
Full demonstration kits, including interface boards that connect the inverter board to the controller board development tool are available to reduce design times with fast prototyping.
The default setting for the GaN-based motor drive kit is 100kHz switching frequency and 14ns deadtime. The kit is designed to be programmed for different frequencies and deadtimes, and its operation at high frequency (around 100kHz) eliminates electrolytic capacitors, enables and the use of lower capacitance and reduces the motor losses. Operating the boards with a low deadtime allows higher torque per Ampere. Combined these characteristics improve inverter and motor system efficiency of more than 7% compared with a silicon MOSFET which typically operates at 20kHz and 500 ns deadtime, reports EPC.
Both the EPC9167 and the EPC9167HC reference designs are available from immediate delivery from distributor, Digi-Key Electronics.
View PDF
| Privacy Policy | Site Map | © Copyright DFA Media
| Web design by Immersive Media