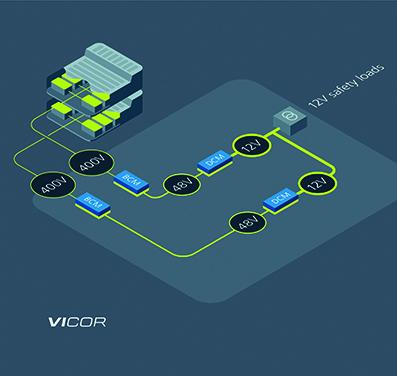
BEV advancements are driving sales, but vehicle safety and reliability will ensure long-term viability
Innovative power architectures using power modules provide power redundancy and improve overall safety and system performance By Patrick Kowalyk, Automotive FAE,Vicor
More details...
A full brick package developed by TDK-Lambda, the PF1500B-360, is for high voltage distributed power architectures
More details...
The Cell2Pack demonstrator showcases the future of structural battery design for niche market and low volume applications in the automotive sector, says the company.
The structural battery pack system features host of advances which combine to improve electric vehicle structural stiffness, lower weight and improve overall range, at low production volumes.
Cell2Pack is a specific battery design for the automotive niche market and low volume applications of under 10,000 vehicles per annum. The cells are integrated directly into the battery pack without the need for individual module enclosures, increasing volumetric energy density and improving vehicle range within a given package. To achieve a high level of integration, the cells become a load-bearing element and provide a load path directly through the battery pack from base-to-lid, and into the vehicle body.
The Cell2Pack system incorporates advanced technical features such as large format cylindrical cells, inflatable side cooling and a bent extruded case.
The large format cylindrical cells reflect the industry’s move towards larger format cylindrical 46xx cells which offer high power and energy density, as well as increased fast charging capability due to reduce internal resistance.
Flexible and inflatable side cooling ribbons offer double-sided cooling to the cells. The adaptive flexible shape ensures close contact with the cells without the need for gap fillers or thermal interface material, improving heat transfer from the cells to the coolant. Manufacturing is also simplified with no need to attach the cooling ribbons to the cells.
There is also a continuous 3D bent extrusion which forms three sides of the battery case with a clip fit panel base. This design enables the package length and width to the scaled to the customer requirements without the need for high-cost tooling changes, suitable for low volumes, says the company.
View PDF
| Privacy Policy | Site Map | © Copyright DFA Media
| Web design by Immersive Media