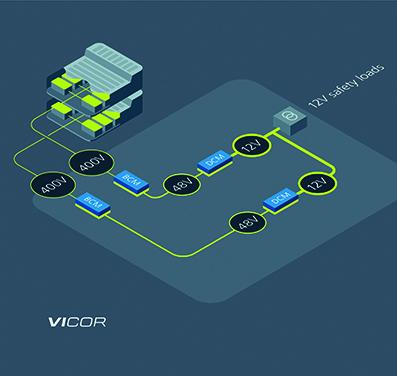
BEV advancements are driving sales, but vehicle safety and reliability will ensure long-term viability
Innovative power architectures using power modules provide power redundancy and improve overall safety and system performance By Patrick Kowalyk, Automotive FAE,Vicor
More details...
A full brick package developed by TDK-Lambda, the PF1500B-360, is for high voltage distributed power architectures
More details...
The EPC9194 GaN-based inverter reference design enhances motor drive system efficiency, range, and torque and more than doubles power density, says the company. It is compact, for seamless integration into the motor housing to yield what is claimed to be the lowest EMI, the highest density and lowest weight.
The company offers the EPC9194 three-phase BLDC motor drive inverter reference design which operates from an input range of 14V to 60V and delivers up to 60A pk (40A RMS) output. These characteristics make it suitable for various three-phase BLDC motor drives including e-bikes, e-scooters, drones, robots, as well as DC servo motors.
The EPC9194 demonstration board features six EPC2302 100V eGaN FETs in a 3.0 x 5.0mm QFN package. The board measures just 130 x 100mm, including the connector. The EPC2302 eGaN FET offers a small RDS(on), of just 1.8mΩ, combined with very small QG, QGD, and QOSS contributing to reduced conduction and switching losses. The package is a thermally enhanced QFN with exposed top for enhanced heat dissipation to the heatsink, and wettable flanks for easy inspections.
With a 48V input and 100kHz PWM frequency, the board can deliver 20A RMS steady state without heatsink with a temperature rise of 60°C, and more than 30A RMS with a heatsink.
The estimated total power loss with six EPC2302 (20A RMS/100kHz PWM) is half that of a Si MOSFET solution with the same RDS(on) operating at 16kHz PWM frequency, says EPC. The 100kHz PWM frequency enables a quasi-pure sinusoidal current, reducing vibration and distortion in the motor and resulting in about 7% higher motor system efficiency. A PWM frequency of 100kHz allows for the reduction of the input filter and the elimination or reduction of electrolytic capacitors, adds the company.
Critical circuit functions to support a motor driver are incorporated in the EPC9194, for example, gate drivers, regulated auxiliary power rails for housekeeping supplies, voltage, and temperature sense, accurate current sense, and protection functions.
The EPC9194 is compatible with various controllers from different manufacturers for quick development and reduced design cycle times. EPC offers control interface boards (EPC9147X) to operate this inverter reference design with common BLDC motors. The EPC9194KIT includes the EPC9194 evaluation board and a controller board that allows to easy interface the board with a microcontroller design kit:
Variations are the EPC9147A controller board to interface to popular Microchip microcontrollers, the EPC9147C controller board to interface to popular ST microcontrollers, the EPC9147B controller board to interface to popular TI microcontrollers and the EPC9147E controller board to interface to generic microcontrollers.
The EPC9194 reference design board is available for immediate delivery from Digi-Key.
Designers interested in replacing their silicon MOSFETs with a GaN solution can use the EPC GaN Power Bench’s online cross-reference tool to find a suggested replacement based on their unique operating conditions.
View PDF
| Privacy Policy | Site Map | © Copyright DFA Media
| Web design by Immersive Media