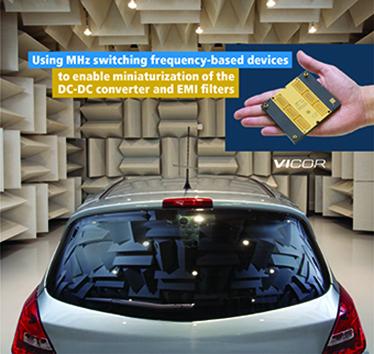
MHz switching frequency-based devices enable miniaturization of the DC-DC converter and EMI filters
Achieving EMI conducted emission compliance for automobiles with a single stage filter. By Nicola Rosano, Sr. Strategic FA/System Engineer at Vicor
More details...
A full brick package developed by TDK-Lambda, the PF1500B-360, is for high voltage distributed power architectures
More details...
Field Lifetime Estimation of Power Modules using Active Power Cycling
The design of power electronics modules and power packages is heavily influenced by thermal concerns. New substrate materials, thinner and thermally more conductive attachment materials are used to decrease the thermal resistance of a given module. When a new material or technology is applied, its reliability has to be tested thoroughly before the module can be considered for production.
The two commonly used lifetime tests for power modules are Temperature Cycling and Active Power Cycling. Both test methods introduce a thermal load by periodically changing the device temperature, but are fundamentally different.
In Temperature Cycling the device is unpowered. Temperature change is achieved by placing the part in a thermostatically-controlled environment such as an oven, which both heats and cools the part. Hence the heating is externally applied. The heating and cooling rates are relatively slow, of the order of several minutes, so the temperature within the part remains fairly uniform as it heats and cools. Temperature Cycling is mainly used to evaluate solder joints between the Direct Bonded Copper (DBC) substrate and the module’s baseplate.
By contrast, in Active Power Cycling the part is heated internally, by passing current through the semiconductor device, thereby using it as a dissipating element. Heat is dissipated at the same location heat is dissipated during normal operation, resulting in a temperature distribution within the part that is similar to the application. As the heating is localized, significant temperature gradients result. These can be controlled by changing the rate of heating by changing the supplied current.
The most frequent cause of failure of a power module is the cracking or delamination of different layers due to the thermally-induced stresses that arise from periodic cycling. The magnitude of the thermal stress is proportional to the temperature change induced by the power dissipated by the semiconductor devices. Consequently the next step is to turn the P(t) mission profile into a temperature vs. time function. As the dissipation is not constant, but rather a complex time function, the temperature function cannot be analytically calculated either. Most modern 3D thermal simulators can do transient simulations, and there are some that can handle arbitrary dissipation profiles as well. Even in case of quite complex package structures a detailed 3D model can be built using Mentor Graphics software.
More in our upcoming online and printed issue
| Privacy Policy | Site Map | © Copyright DFA Media
| Web design by Immersive Media