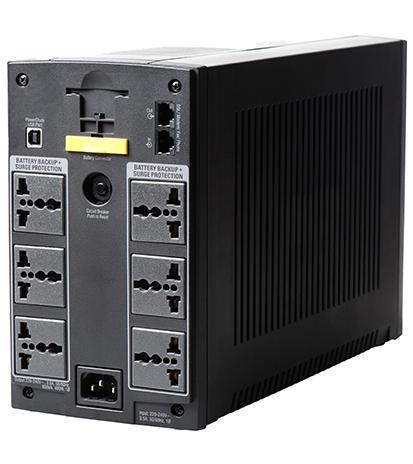
Comparing N-Channel and P-Channel MOSFETs: Which is best for your application?
This article compares the n-channel and p-channel power MOSFETs, introduces the complete Littelfuse p-channel power MOSFETs portfolio, and explores target applications.
More details...
A full brick package developed by TDK-Lambda, the PF1500B-360, is for high voltage distributed power architectures
More details...
Dillenburg-based Isabellenhuette is now transferring its already 1903 invented Half Heusler metallurgy compound into reality for regenerating waste heat into electrical power. PEE was given the opportunity to take a first look on the pilot line featuring an investment of €1 million.
Transport, notably automotive, and process industries, in particular metallurgy, glass and chemicals, are today responsible for a large amount of waste heat above 140°C, estimated to reach 5 000 GWh/year, worldwide. Directly generating electricity from waste heat by means of thermoelectric generators could therefore significantly reduce the global carbon footprint of these activities. However, thermoelectric materials have not yet found their way into mass markets due to lack of sustainable sources of materials for production, progress to be made on the required material performance and an industrial production capacity.
Radioisotope thermoelectric generators were developed already in the 1980’s for the Voyager spacecrafts, Voyager 1 and Voyager 2. Conversion of the decay heat of the plutonium to electrical power used 312 SiGe thermoelectric couples which supplied the spacecraft with 470 W at launch.
NASA chose to use a nuclear power source because solar power alternatives did not meet the full range of the mission's requirements. Only the radioisotope power system [the RTG] allows full-time communication with the rover during its atmospheric entry, descent and landing regardless of the landing site. And the nuclear powered rover can go farther, travel to more places, last longer, and power and heat a larger and more capable scientific payload compared to the solar power alternatives. Also the Curiosity rover that has been exploring Mars since August 2012 is supplied with thermoelectric power, and the Mars 2020 mission will obtain its electrical power from a radioisotope power system called a Multi-Mission Radioisotope Thermoelectric Generator (MMRTG). A MMRTG converts the heat created by naturally decaying plutonium-238 into electricity that can be used to run a spacecraft and its science instruments.
Radioisotope power systems enable or enhance missions where sunlight is infrequent, obscured by dust, or dimmed by distance, making other sources of power impractical or insufficient. But this technology is not usable for civil applications such as transportation or power plants since it relies on radioactivity.
Now German Isabellenhuette has explored a safer way to recover waste heat i. e. of combustion engines by using its already 1903 invented Half Heusler Compounds. It contained two parts copper, one part manganese, and one part tin (Cu2MnSn). Its magnetism varies considerably with heat treatment and composition. Room-temperature saturation induction is around 8,000 gauss, which exceeds that of the element nickel (around 6100 gauss) but is smaller than that of iron (around 21500 gauss).
The company with its over 900 employees is one of the world’s leading manufacturers of electrical resistance and thermoelectric materials for temperature measurement and passive components in the automotive, electrical and electronics industries. Precision measurement systems set the industry benchmark for current, voltage and temperature sensing in cars and trucks, hybrid and electric vehicles, as well as industrial and renewable energy generating systems. The company has been working since 2009 on the synthesis of thermoelectric Half Heusler compounds with a melt-metallurgical manufacturing process. Since 2015 Isabellenhuette is working on the development of thermoelectric modules based on Half Heusler material and brought its experience in an EU project INTEGRAL (waste heat to power) comprising European research and industrial partners. The project has received funding from the European Union’s Horizon 2020 research and innovation program.
INTEGRAL covers industries, small enterprises, research centres with various expertise required for the success of the project such as experts in thermoelectric generators for automotive heat recovery from Valeo (France); Experts in industry heat waste from Elkem (Norway) and autonomous temperature control in industry with ArcelorMittal (Spain); Nanostructured Material production by high energy ball milling with MBN Nanomateralia (Italy); Silicon thermoelectric ring design and production with Hotblock On Board (France); Cast silicon thermoelectric modules with strip-legs design and production with RGS Development (The Netherlands); Thermoelectric material customisation for thermal and electrical conductivity with Cidetec (Spain); Thermoelectric generators prototyping line, as well as material shaping and tuning, and in-line process control with the POUDR'INNOV 2.0 Powder Metallurgy Platform at CEA Liten (France); Sintering and off-line ageing and characterisation with Fraunhofer IKTS (Germany); new material life cycle analysis and cost targeting with Efficient Innovation (France); and Half Heusler cubic-legs design and production with Isabellenhütte (Germany).
The aim of the INTEGRAL project is to upscale a new generation of thermoelectric technology, using existing and growing pilot industry lines, in order to address mass markets (transport, process industries), and to produce advanced functional materials with customized electrical and thermal conductivities. The INTEGRAL project is unique since it gathers leading companies developing these materials in Europe. Furthermore, the large-scale manufacturing processes to be developed for producing nanostructured materials within the project cut across multiple sectors to find a wide range of applications outside thermoelectrics, i.e. where customization of electrical or thermal properties of sintered or casted materials is needed. Finally, a technology transfer will be performed towards the commercialization of a new generation of advanced multifunctional materials with a circular economy vision.
In this context Isabellenhütte is exploring its Half Heusler cubic-legs design in an automated pilot line for mass production for up to 30,000 modules annually. Module size is 150 mm x 100 mm, 1 cm² of module size will harvest around 1 W of electrical power. “Fifty percent of system cost for such an energy harvester consist of the thermal modules, and thirty percent of these are the miniature cubic legs. So far the modules were built more or less manually, but with our newly automated production line we are able to cut cost significantly. We have already synthesized 10 kg of appropriate Half Heusler material in an oven taking around two days, later we will exceed the capacity to 25 kg. The material will then be sawed, sliced and polished. The tiny cubic-legs are then assembled via pick-and-place machine onto the substrate, which is mounted onto the cold plate”, said R&D director Dr. Jan Marien. “Typical applications are automobiles, where electrical power is generated within the exhaust gas stream at temperatures around 600°C. Particularly for mild hybrids we envision an additional recuperation of up to 500 W for around 50 Cent/W.” AS
More in our July/August issue.
| Privacy Policy | Site Map | © Copyright DFA Media
| Web design by Immersive Media