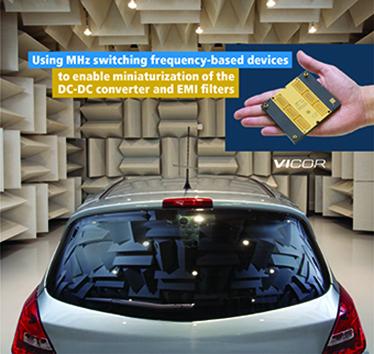
MHz switching frequency-based devices enable miniaturization of the DC-DC converter and EMI filters
Achieving EMI conducted emission compliance for automobiles with a single stage filter. By Nicola Rosano, Sr. Strategic FA/System Engineer at Vicor
More details...
A full brick package developed by TDK-Lambda, the PF1500B-360, is for high voltage distributed power architectures
More details...
Silicon Carbide is now commonly accepted as a reliable and pertinent alternative to the Silicon world. Most power module and power inverter manufacturers have already included it in their roadmap as an option or as a firm project. However time-to-market differs from application to application. Despite a quite depressed market last year, PV inverters have proven their appetite for SiC devices in 2012. They are the biggest consumer of SiC devices together with PFCs. In 2011 and 2012 SiC diode business was the most buoyancy due to microinverter applications, but according to market researcher Yole both JFET and MOSFET will quickly catch-up and become dominant in revenue by 2016. SiC device (bare-dies or packaged discretes) market reached about $75 million in 2012 with a sharp domination by Infineon and CREE, however the competition is little by little grabbing market share with STMicroelectronics and ROHM closing the loop. Most recently Ixys and Toshiba entered the market with SiC diodes.
There are now more than 30 companies worldwide which have established a dedicated SiC device manufacturing capability with related commercial and promotion activities. Virtually, all other existing Silicon-based power device makers are also more or less active in the SiC market but at different stages. 2012 has seen the ramp-up of some companies, such as Rohm, MicroSemi, GeneSiC or STMicro, facing the giants CREE and Infineon, prefiguring a new market shaping in the coming years. Four new companies - Raytheon, Ascatron, IBS and Fraunhofer IISB - have decided, almost simultaneously, to launch SiC foundry services or contract manufacturing services. This business model establishment addresses the demand of future SiC fabless and design houses that may look for specific manufacturing partners. It will also probably act as a possible second source for IDMs in cases of production overshoot. Power device integrators generally rely on two, or even three sources to lower supply-chain risks. In SiC, it is now easy operating multisourcing for diodes, though not yet for transistors.
We have reported on the achievements in SiC and also GaN extensively, but at every conference progress can be noted. AT EPE ECCE 2013 early September in Lille Virginia Tech presented a paper comparing the static and dynamic characterizations results of various SiC devices for temperatures ranging from 25 to 200°C. Specifically, commercial and sample transistors from Cree, GE, ROHM, Fairchild, GeneSiC, Infineon, and SemiSouth (disappered from the market) were tested. The results showed that the ROHM SiC MOSFET and Infineon SiC normally-on JFET had the highest specific on-resistances (based on the total die area), while the Fairchild SiC BJT experienced the lowest. The on-resistance of the BJT also proved to have the weakest temperature dependence. Regarding the dynamic characterization results, SemiSouth’s SiC normally-off JFET showed the lowest total switching energy losses when plotted against load current, that's why this device was referenced in various PV inverter prototypes.
The PEMC group of the University of Nottingham presented results of SiC Power MOSFETs in PV inverters. In particular, their stable performance against switching frequency and temperature enables high flexibility in overall system design, trading off between efficiency and power density requirements and goals. The results of the benchmarking exercise between an all SiC and a mixed Si/SiC solution indicates that use of a mixed SiC and Si solution, with IGBTs and Schottky diodes as the bi-directional switch, is competitive in performance to that of a fully SiC Power MOSFET based on relatively low heat-sink temperatures and switching frequencies, with severe limitations on design flexibility and optimization at system level. Also, the results point out interest in the availability of SiC power MOSFETs in voltage classes lower than 1.2 kV, too, for the needs of bi-directional switched neutral-point-clamped (BSNPC) three level inverter, in which, for the first time, SiC Power MOSFETs of different voltage ratings (1200 and 600 V) are used. Indeed, here, if reference is made to a comparison of 600 V IGBT with Schottky diodes against 600V SiC MOSFETs alone, the additional cost burden due to SiC as opposed to Si can be realistically estimated to be a factor 2 to 3 (keeping in mind that IGBTs require a higher current rating diode, as discussed above) for the implementation of the bi-directional switch. Such cost difference is readily compensated mainly by an increase of the switching frequency which enables a significant reduction of the output filter inductor value.
One of the main benefits of SiC devices is their high temperature operating capability which makes them very attractive for power electronics solutions with operating junction temperature above 180°C The package of a conventional power module represents one of the main bottlenecks to fully exploit the high temperature capability of the SiC devices. A first step to operate at high temperatures is improved reliability of the ceramic substrate and die attach at elevated temperatures. Thus ABB assessed selected materials and assembly technologies for power modules with the capability to operate at high temperatures. According to the research Si3N4/Cu ceramic substrates showed the best robustness against aggressive liquid-liquid thermal shock cycling in the interval of -50°C to 190°C. No delamination of Cu-metallization was observed after 2500 cycles and only a very small increase of the surface roughness was detected. A sintered SiC die attach was also without typical edge delamination up to tested 1500 cycles. AlN/Al DBA and AMB substrates were less robust against cycling compared to Si3N4/Cu substrates. On the other hand only very weak delamination of the sintered chips was observed despite a significant increase of the surface roughness.
Bosch gave a paper which for the first time the interactions of a copper metallization with a SiC device analyzed and optimized with respect to an interconnection via copper wire bonds. In this aspect a multilayer structure with an AlSiCu adhesion promoter and a TiN diffusion barrier as well as a 23 μm thick electroplated copper layer, showed the best performance in the peel-tests, in the bonding test as well as in the passive temperature cycles. Long time annealing experiments at 250°C indicate only very slow reactions between the copper and the SiC device, which generally proves reliable application of the SiC semiconductor with a Cu-metallization at temperatures up to 250°C. With respect to the temperature storage and passive temperature cycles, no significant degradation of the Cu wire-bond connection could be measured. A copper metallization together with copper wire bond connections are a very promising interconnection technology for improving the lifetime and enabling higher junction-temperatures of SiC devices up to 250°C.
Thus SiC could become an alternative to Silicon, but as always the Silicon empire strikes back!
In our September issue some more achievements in SiC are presented.
| Privacy Policy | Site Map | © Copyright DFA Media
| Web design by Immersive Media